How Portland Public Schools achieved an 80% time reduction
FME Automation achievements
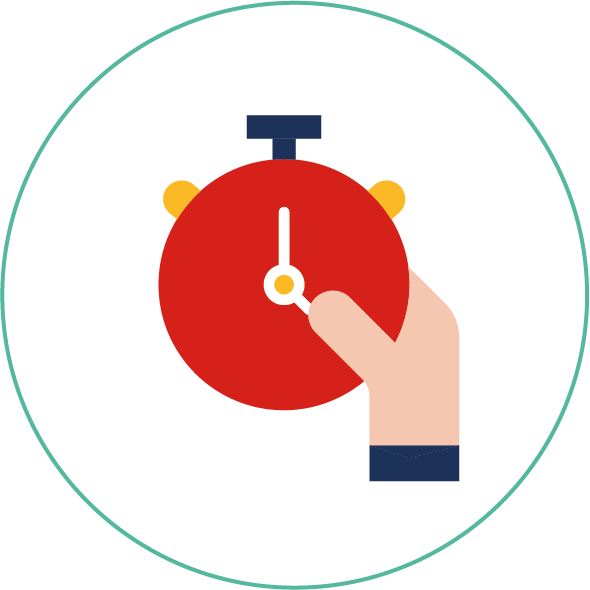
TRIRIGA data update time slashed by 80%
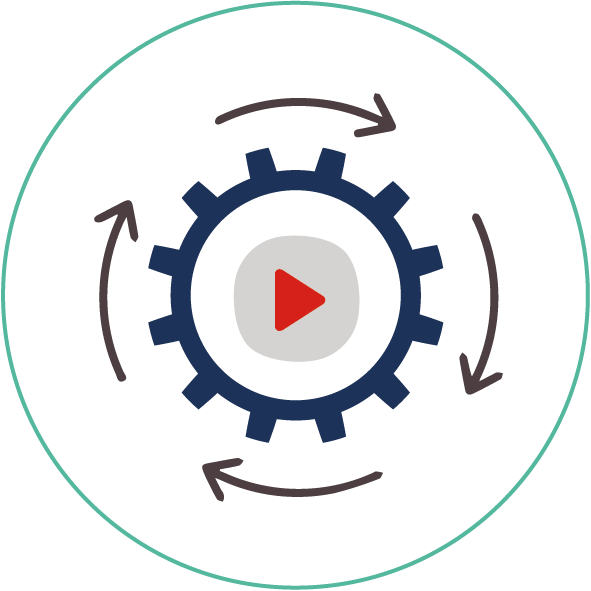
200 hours saved annually through automation
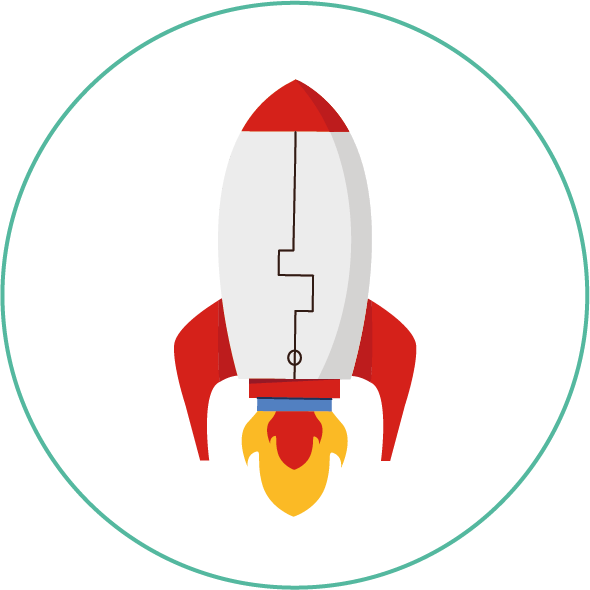
99% quality assurance ensuring GIS performance
The background
Portland Public Schools (PPS) is one of the largest school districts in the Pacific Northwest.
With more than 49,000 students in 81 schools, PPS provides rigorous, high-quality academic learning experiences that are inclusive and joyful. The Planning and real estate team operates to support the district’s mission by providing a safe and healthy environment that is conducive to learning for students and staff.
The Planning and Real Estate team uses a cutting-edge solution called IBM TRIRIGA as their Computerized Maintenance Management system (CMMS) to maximize operational efficiency in managing facilities and real estate. With IBM TRIRIGA, they can centralize asset data, track operation costs, automate maintenance workflows, maximize space use, manage moves and much more.
The challenge
In order to offer high value-added features, TRIRIGA uses a data structure that differs from the standards used in the GIS industry, which makes access to information complicated for non-expert users and analytics impossible. In addition, the existing methodology for integrating CAD to GIS was time consuming and challenging to troubleshoot. The integration between TRIRIGA and GIS was a manual static connection that led the data to be inconsistent between systems.
PPS’s Planning and Real Estate team opted for an integration-based strategy to automate the transfer of CAD data and to sync TRIRIGA with ArcGIS in order to:
- Minimize data silos within the organization
- Improve collaboration, efficiency and decision making
- Ensure that data is shared and accessible by other departments
- Make TRIRIGA information more accessible to non-expert users
- Make it possible to create reports and dashboards directly from the ArcGIS database
- Make it easier to transfer data between TRIRIGA and the organization’s other systems
- Automate the existing workflows and integrate QA/QC into the workflow
After years of unsuccessful scripting-based integration attempts, the PPS team turned to Consortech’s low-code FME experts for help.
The solution delivered
Before rolling up our sleeves and diving into such a complex project, we needed a feasibility study. We chose a collaborative proof of concept so we could combine the client’s knowledge of their own internal data and processes with Consortech’s application integration expertise. The Consortech team and the PPS Planning and Real Estate team worked together through multiple iterations to create an integration project plan that included a statement of work with an in-depth outline of the project’s stages, from delivery milestones to a detailed breakdown of total project costs.
Once the full integration project was approved, Consortech’s project lead enlisted a multidisciplinary team of two FME developers and one solution architect. Of course, Consortech was entirely in charge of the project, but it was important to keep the other three stakeholders (the client, the subcontractors who manage ArcGIS, and the subcontractors who manage TRIRIGA) closely in the loop throughout.
We created a completely automated process, without a single line of code, on the development side to sync up the three systems (ArcGIS, TRIRIGA and CAD) on a daily basis.
A few numbers to give you an idea of the magnitude of the project:
- 7 FME Form workspaces developed
- 3 FME Flow automations deployed
- 1 FME Flow app gallery created to manually trigger the process as needed
- A whopping 1,000+ transformers used
All delivered in 2 distinct environments (UAT/PROD) to guarantee greater stability
during maintenance and the development of future enhancements to the solution.
Gains
From CAD data to TRIRIGA with a reliable ArcGIS: daily syncs for better insights!
Despite the challenge of coordinating the work of four different stakeholders, the project was delivered on time and on budget. The three environments (CAD, GIS and TRIRIGA) are now synced daily, so the client can ensure the quality of their ArcGIS database and trust that their information is being processed and shared in the best way possible.
The project also gave the PPS team better insight into the structure of the data in TRIRIGA, so they can now integrate additional TRIRIGA data to provide analytics for our users and leadership for data driven decision making in asset and facility management.
Time and Quality Gains
A quality assurance of at least 99% for all spaces to be accounted for in TRIRIGA and coordinated with Maps & GIS. Higher confidence in our data because QA/QC is automated and allows us to find inconsistencies before the data is available to our users.
The time it takes to make data updates in TRIRIGA has been reduced by 80%. Updating a data table in TRIRIGA would normally take 2 days at minimum and now takes a couple hours to prep and change. Now, updates can happen in the GIS system and update with automated syncing using FME.
Hours gained through our TRIRIGA software integration
100 hours of annual time for CAD integration. The time it would require to clean, edit, integrate and troubleshoot new or edited DWGs with the GIS Analyst.
50 hours annually, for auditing purposes. The time it would normally require to search for inaccuracies by process of elimination. The automated FME reports provide an inventory of existing spaces that are missing polygons in CAD and are therefore reporting on the inaccuracies rather than requiring us to search for them.
50 hours annually for Data changes or updates as the FME tool also provides us with constant report capabilities to find inconsistencies in our updates of Tririga, CAD and CAD to GIS coordination. Space is getting removed or the space use changes – coordinating and updating with the GIS analyst is no longer necessary.
Despite facing budgeting constraints, challenges with TRIRIGA’s Data structure, and involvement from multiple vendors, we embraced the transformative power of expert guidance. With Consortech, we found a partner who not only helped us navigate these obstacles but elevated our department’s analytical capabilities. Through their innovative solutions, they were able to create a dynamic and beautifully crafted system. As a result, Consortech propelled our group forward, forging connections between data structures once thought to be uncommunicative. The impact has been extraordinary, with our analytic and data management capabilities experiencing a remarkable increase since utilizing FME to integrate and transform our data.